Glass is a material we see every day, from windows and bottles to mirrors and screens. But have you ever wondered how glass is made? The process of making glass is fascinating and involves several key steps. In this article, I will walk you through the main processes involved in a glass factory. You’ll see how raw materials are transformed into the clear, durable glass products we use in our daily lives.
Gathering Raw Materials
The first step in making glass is gathering the raw materials. The primary ingredients used in glassmaking are sand, soda ash, and limestone. Sand, or silica, is the most important component. It provides the bulk of the glass and gives it its strength. Soda ash, or sodium carbonate, lowers the melting point of the sand, making it easier to work with. Limestone, or calcium carbonate, helps to stabilize the mixture and improve the durability of the final product.
These materials are usually delivered to the glass factory in bulk. They are stored in large silos or storage bins until they are needed. The raw materials must be carefully measured and mixed in the correct proportions to ensure the quality of the glass. Any impurities in the materials can affect the clarity and strength of the glass, so it’s essential to use high-quality ingredients. This stage is crucial because the quality of the raw materials directly impacts the final product.
NOTE: Looking for the best Dubai glass factory? GLASSMIRROR offers exceptional quality and craftsmanship for all your glass needs. From windows to custom designs, we provide durable and beautiful glass products. Visit us today to explore our wide range and transform your space with stunning glasswork. Contact GLASSMIRROR now!
Mixing and Melting
Once the raw materials are gathered, they are mixed together and melted. The mixing process ensures that the materials are evenly distributed and ready for melting. This mixture is then fed into a furnace where it is heated to extremely high temperatures, typically around 1700 degrees Celsius. This intense heat causes the materials to melt and fuse together, forming a liquid known as molten glass.
The furnace is one of the most critical parts of a glass factory. It must maintain a consistent temperature to ensure the glass melts evenly. Any fluctuations in temperature can cause defects in the glass. This molten glass is kept at a high temperature to keep it in a liquid state, allowing it to be shaped and formed into various products. The melting process can take several hours, depending on the type of glass being produced.
Forming the Glass
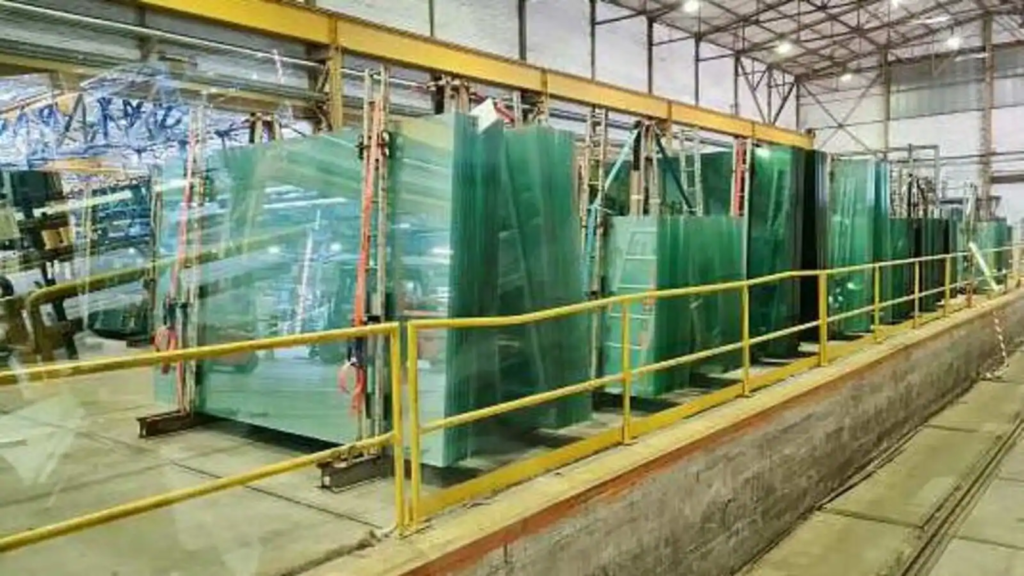
After the raw materials have melted into molten glass, the next step is forming. This is where the glass begins to take shape. There are several methods used to form glass, each suited to different types of glass products. One of the most common methods is called the float glass process, used to make flat glass for windows and mirrors. In this process, the molten glass is poured onto a bed of molten tin. Because glass floats on the tin, it spreads out to form a flat, even surface. The glass is then slowly cooled to prevent it from cracking or breaking.
Another method is blowing, which is used to make bottles and jars. In this process, a gob of molten glass is placed into a mold and then air is blown into it, causing the glass to expand and take the shape of the mold. This method allows for the creation of various shapes and sizes. There is also the pressing method, where molten glass is pressed into a mold to form objects like dishes and lenses.
Annealing Process
Once the glass has been formed, it needs to be slowly cooled in a process called annealing. This step is essential because it helps relieve the internal stresses that can develop in the glass as it cools. If glass cools too quickly, it can become brittle and prone to breaking. During the annealing process, the glass is passed through a long, temperature-controlled oven called a lehr. The temperature in the lehr gradually decreases, allowing the glass to cool slowly and evenly.
The annealing process can take several hours to several days, depending on the thickness and type of glass being produced. Proper annealing is crucial to ensure the strength and durability of the glass. It’s a delicate process that requires careful monitoring and control. If the glass isn’t annealed correctly, it can develop internal stresses that could cause it to break or shatter later on.
Cutting and Shaping
After the glass has been annealed, it’s ready to be cut and shaped into its final form. This step involves cutting the glass to the desired size and shape using various tools and techniques. For flat glass, such as window panes and mirrors, the glass is cut using a diamond or carbide-tipped tool. This tool scores the surface of the glass, creating a line that allows the glass to be snapped along the score.
For more complex shapes, such as bottles and jars, the glass may be further shaped using grinding and polishing techniques. This can involve removing any rough edges or imperfections to create a smooth, finished product. Cutting and shaping are done with precision to ensure the glass meets the required specifications. This step requires skilled workers who can handle the glass carefully and accurately.
Quality Control
Quality control is an essential part of the glass-making process. Throughout each stage, the glass is carefully inspected to ensure it meets the required standards. This includes checking for any defects, such as bubbles, cracks, or inclusions. Any glass that doesn’t meet the quality standards is rejected and either re-melted or discarded.
Quality control also involves testing the physical properties of the glass, such as its strength and durability. This can include various tests, such as impact resistance, thermal shock resistance, and optical clarity. Ensuring high quality is crucial because glass products must be safe and reliable for their intended use. The quality control process helps ensure that only the best glass products make it to the market.
Finishing Touches
The final step in the glass-making process is applying any finishing touches. This can include adding coatings or treatments to the glass to enhance its properties. For example, some glass products may be coated with a reflective or anti-reflective coating to improve their optical performance. Others may be treated with a protective coating to enhance their durability and resistance to scratching.
Finishing touches can also involve decorating the glass, such as adding patterns or designs. This is often done using techniques like etching, sandblasting, or screen printing. These finishing touches can add both aesthetic appeal and functional benefits to the glass products. The goal is to create a final product that not only looks good but also performs well for its intended use.
Packaging and Shipping
Once the glass products are finished, they are carefully packaged and prepared for shipping. Packaging is crucial to protect the glass during transportation and ensure it arrives at its destination in perfect condition. This often involves using protective materials, such as foam, cardboard, or plastic, to cushion the glass and prevent it from breaking.
Shipping glass products require careful handling and coordination. Glass is fragile and can easily be damaged if not handled properly. Special care is taken to ensure the glass is securely packed and transported. This can involve using specially designed crates or containers to protect the glass during transit. The goal is to deliver the glass products safely and efficiently to their final destination.
Conclusion
The process of making glass involves several key steps, each requiring precision and care. From gathering raw materials to packaging and shipping, each stage is essential to producing high-quality glass products. By understanding the key processes involved in a glass factory, you can appreciate the skill and craftsmanship that goes into making the glass products we use every day. Whether it’s a simple windowpane or an intricate glass sculpture, the journey from raw materials to finished product is a fascinating and complex one.
For More Isightful Articles Related To This Topic, Feel Free To Visit: blooketlogin